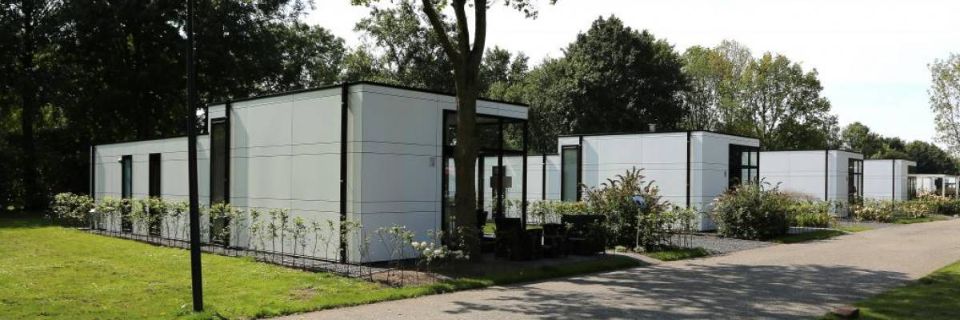
A modular approach to construction
How the benefits of 'Prefab' are reaching a wider audience
The ‘modular’ method of construction involves prefabrication of sections, which are delivered to buildings site for further processing. According to European commission research, technology-driven standardization and industrialization of building processes and offsite construction result in “a 30% reduction in project costs and a 40% shortening of completion times.” The standard of building and finishing is no different than that of ‘regular’ building works. Three Trespa clients share their experiences and expectations of modular construction, and explain where they see the advantages.
WANDERS MOBIELE CHALETS
“Wanders Mobile Chalets is one of the Netherlands’ largest custom builder of high-quality and luxury recreational
homes, informal care homes and caravans. Every year, some 400 homes nd their way to Dutch, German, Belgian and Swiss holiday parks and individual clients. Buildings can be tailor-made based on customer preferences or created in series. Everything in the building is supplied complete by Wanders, including kitchens, bathrooms, toilets, tted wardrobes, and more.”
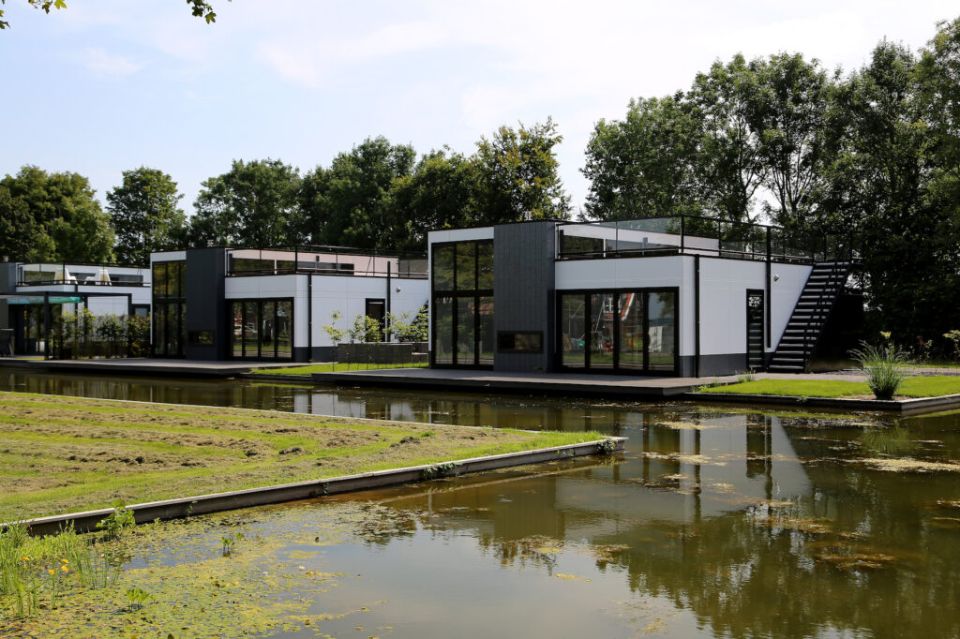
“We use a modular construction approach for all of our products. Parts are connected on site to create single and multi-storey houses. Because everything is prefabricated in a controlled environment, no lengthy construction processes are required. Disruption for residents, noise pollution and CO2 emissions on site are also minimized and deliveries are fast and short. Bad weather or frost doesn’t affect working times or product quality. e speed and other bene ts of this approach have even allowed us to expand into regular housing market target areas, such as smaller homes for starters.”
“Trespa’s products is used for façades. is type of cladding is extremely suitable for houses with a contemporary design, with clear lines. Buildings retain their colors and contours without visible wear and tear, whilst requiring minimal maintenance. For us, Trespa® products are practical as they help realize sleek designs and don’t require painting.”
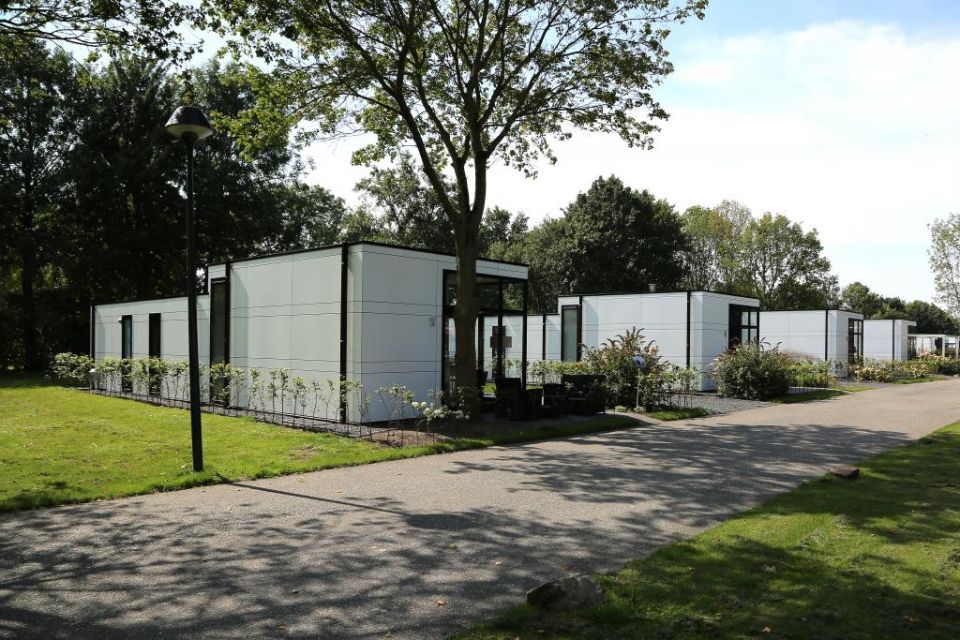
HEINKEL KG MODULBAU UND FAHRZEUGBAU
“We manufacture room modules, and work for all areas of the healthcare sector, as well as industrial and municipal facilities. Modular construction is used to create interior fittings of laboratories and operating theatres, which require high levels of stress tolerance and hygiene, as well as for high quality, maintenance-free façades, which need to withstand mechanical stress. For us, the time factor and high level of quality played a decisive role in the decision to introduce modular building. is way of working also allows us to minimize emissions at the construction site during assembly of prefabricated room modules. is fact is particularly appreciated in the construction of clinics and in the general care sector. We’re seeing that modular construction is no longer used exclusively for small ‘cookie cutter’ buildings in identical series, but also for more luxurious projects on a grander scale.
“Cladding is used in the exact same way as it would be in ‘traditional’ building. We frequently apply Trespa® Meteon® to façades and Trespa® TopLab® for interior fittings of military- grade constructions, in which hygiene is essential, as well as for the protection of walls in highly stressed areas, such as clinic hallways, schools, and daycare centres. Overall, our key reasons for using Trespa® products are the variety of options for architecture, in addition to the low maintenance.”
VERANCLASSIC
“We started out building conservatories and now specialize in habitable spaces adjacent to homes, such as pool houses and other outbuildings. Over the years, these have evolved from utility spaces into rooms in which people can entertain, receive guests, spend quality time on their own or even take in elderly relatives. Our buildings are also often used as office spaces or treatment rooms. The demands placed on such spaces, for example when it comes to insulation, are comparable to the demands placed on of houses.
“Structural elements required to create each of our unique buildings are partly created in our workshops, using a modular approach. Prefabricated components are transported to the site where the work is finished. For us, the key benefit is the speed of construction. We can complete a 70-100 m2 building in two to five days. In the past, customers would have large amounts of materials and builders in their garden for two or three months, as structures were built in layers and many different disciplines were called for. By preparing as much as possible off-site we save a significant amount of time.
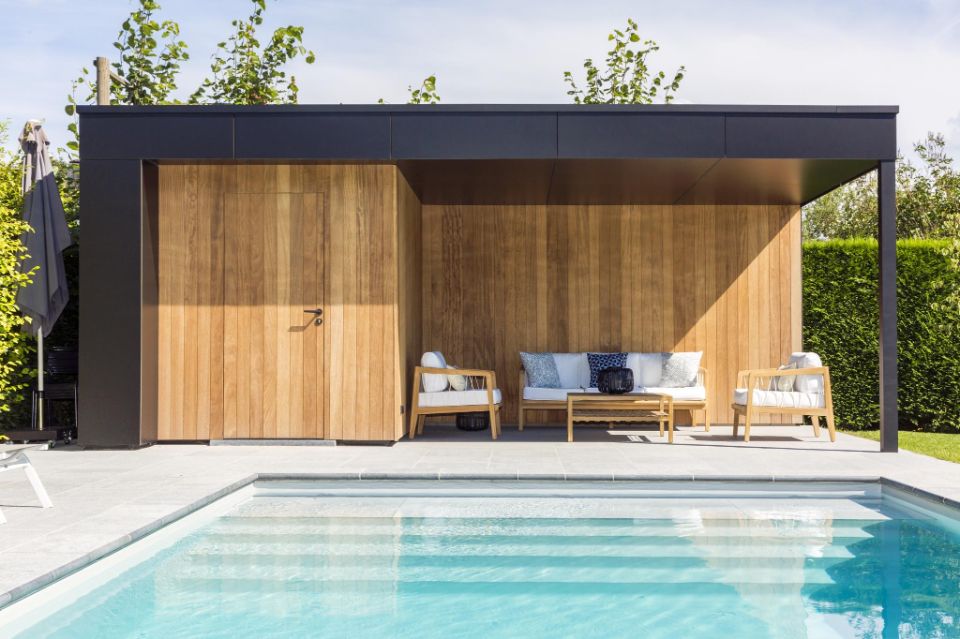
TRESPA® DISTRIBUTOR
“Veran asked us for a material that was long lasting and robust, came with a warranty, wouldn’t lose its surface coating, was highly UV resistant and easy to clean. Importantly, they wanted something they could install and not have to worry about anymore. We proposed Trespa® products because it ticked all these boxes, is extremely workable and can be used in many different ways.
We don’t just sell products from Trespa® as a separate material, but as part of a complete concept. We make sure the people working with it know all the possibilities, techniques and tools required for placement. Reactions are positive: Trespa® panels makes work fast, has a great reputation and there is very little waste thanks to clever dimensioning.”