Deaconess Hospital Mannheim
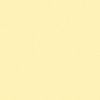
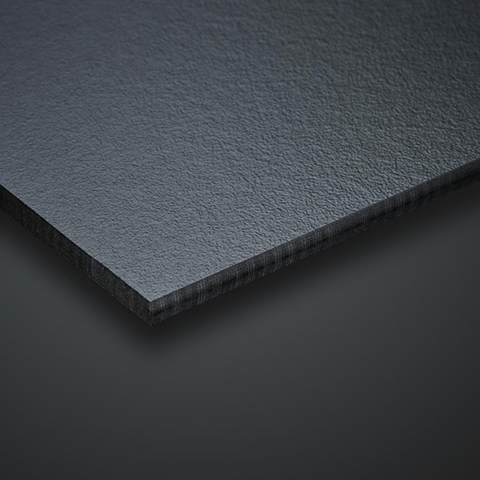
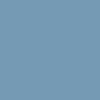
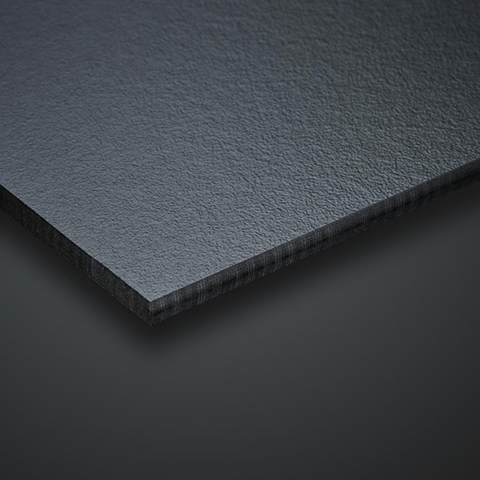
COMBINING HYGIENE, FUNCTION, ERGONOMICS AND VISUAL APPEAL: A NEW OPERATING UNIT SHOWS THE WAY
LOCATED IN THE NORTHERN PART OF BADEN-WÜRTTEMBERG – THE FEDERAL STATE CLOSEST TO FRANCE AND SWITZERLAND – DIAKO MANNHEIM IS ONE OF THE MAJOR HOSPITALS IN THIS AREA OF GERMANY. IT WAS FOUNDED IN 1861 AS THE ‘EVANGELISCHER VEREIN FÜR KRANKENPFLEGE DURCH DIAKONISSEN’. MEANWHILE, THE DEACONESSES ARE LONG GONE AND THE EVENTFUL HISTORY OF THE INSTITUTION – WHICH EVEN INCLUDES A TEMPORARY RELOCATION IN REPURPOSED BARRACKS – HAS GIVEN WAY TO A HEALTHCARE FACILITY THAT CATERS TO 18,000 INPATIENTS AND CARRIES OUT OVER 12,000 SURGICAL PROCEDURES PER YEAR.
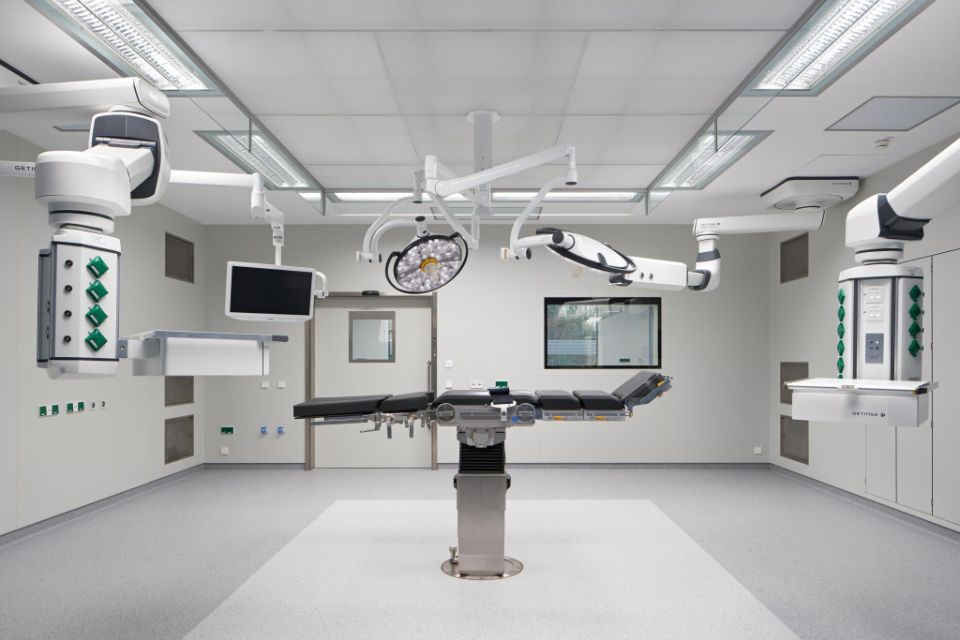
As early as 2012, it had become clear that, as far as the operating theatres were concerned, there was ample room for improvement. The theatres were located wide apart on two different floors, while ancillary areas were in short supply and impractical. As a result, the hospital incurred additional expenses and a variety of inconveniences. To solve these issues once and for all, an ambitious project was initiated: the two operating theatres would be relocated next to each other and complemented by three additional, state-of-the-art theatres. The concept called for a brand new extension: the building permit was requested in October 2017, and the new operating unit was inaugurated in September 2021.
HIGH EXPECTATIONS
Materials used in operating theatres have to meet stringent and numerous requirements. While hygiene is logically of paramount importance, appropriate materials must also be durable, shock-resistant and versatile – i.e. able to meet design requirements in a series of technical contexts. In addition, the materials should be visually attractive. Dörte Krämer works as a project manager at Architekturbüro Roger Strauß, a practice located in Karlsruhe. She was in charge of the project from beginning to end. “We are a specialised, medium-sized architectural firm with a team of about 20. We have been active in the healthcare sector for many years, with a focus on medium-sized projects: in this respect, the extension of the operating centre was typical”. She explains: “When it comes to interior design, we like to rely on High Pressure Laminates from Trespa. We have been familiar with the material for a long time – and we are well aware of its many advantages. HPL panels manufactured by Trespa are highly versatile: they are ideally suited for purposes that range from functional cabinetry and worktops to integrated wall and door solutions. Therefore, Trespa’s TopLab® range has been our material of choice for many projects”.
Hans-Jürgen Neugebauer, the Technical Manager at Diako Mannheim, points out: “The initial recommendation came for the architects. We were keen, though, to keep the users in the loop. This resulted in a working group that brought the planners, the surgeons, the anaesthetists and the medical support team together. This provided all involved parties with the opportunity to discuss the various options in terms of both materials and execution”. He continues: “Our priority, beyond hygiene considerations, was to create an ergonomically adequate workspace, although durability and costs were relevant criteria in their own right”. The wall panels had to be, in addition, fully reversible: in an operating theatre, the walpanels conceal a large amount of technical equipment. All of it had to remain accessible without damaging any part of the structure – to allow, among others, for required retrofits.
AN UNRIVALLED COST/BENEFIT RATIO
Hans-Jürgen Neugebauer was quick to realise that with its TopLab® VERTICAL range, Trespa offered the ideal wall cladding option, with the potential to meet everybody’s expectations. He points out that the material is easy to clean, while being more affordable and significantly more shock-resistant than other panels. Hans-Jürgen Neugebauer considers HPL of Trespa to be a better fit than stainless steel as well: “Uncoated stainless steel is not suitable anymore in operating theatres, especially on large surfaces: with the increasing use of laser-based surgical instruments, unintended reflections could be potentially disastrous. Accordingly, only coated stainless steel would be acceptable – and it is markedly pricier. In this respect, TopLab® VERTICAL panels represent an attractive and definitely appropriate alternative”.
“At the same time, TopLab® VERTICAL can take a lot of abuse without loosing its properties and good looks. With TopLab® VERTICAL, I can be confident for the next 20 years: the material will not disappoint me. This was an essential aspect , because durability was a prerequisite”. Dörte Krämer adds: “With coated metal cabinets and lockers, for example, even small shocks and scratches can result in rust spots – and rather fast. We were not keen to see this happen in such a sensitive environment!”.
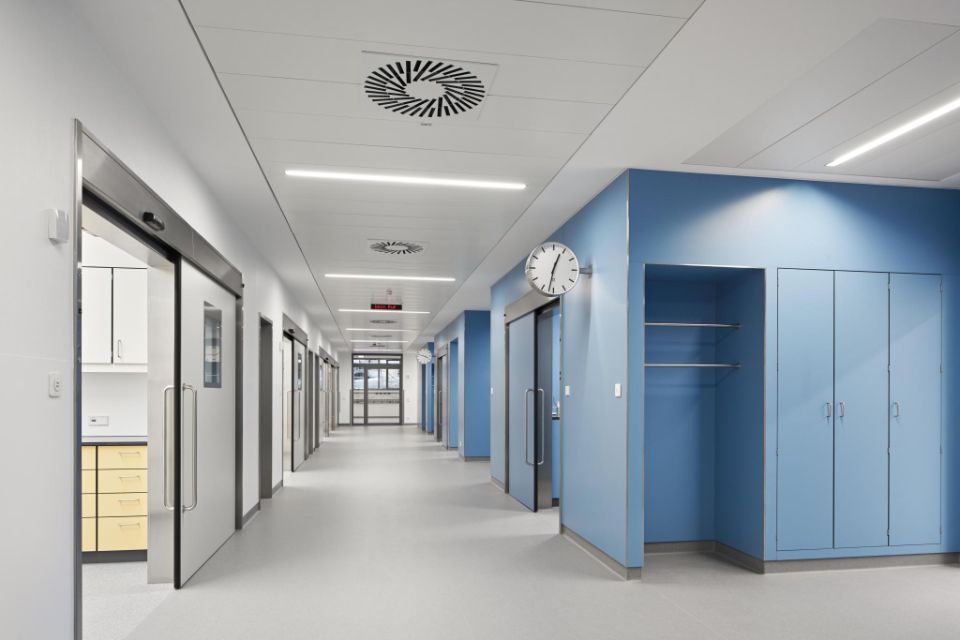
AN UTTERLY COHERENT VISUAL CONCEPT
At Diako Mannheim, Trespa’s TopLab® range did not merely convince in practical terms. The combination of visual appeal and wideranging versatility was a major argument as well. Dörte Krämer comments: “Where stainless steel might have come across as overly technical and ‘clinical’ – to say nothing of the almost unavoidable fingerprints, which tend to make stainless steel look always less than clean – the Trespa® products offer a vast choice of colours. They allowed us to create subtle harmonies throughout the various areas. In this respect, the Trespa® TopLab® range is clearly second to none”.
Hans-Jürgen Neugebauer underscores: “The material enabled us to meet two specific expectations. On one side, we could create a more residential look-and-feel in the ancillary areas: in the past, it was common practice, for example, to install cabinets and lockers with stainless steel doors, which was moderately inviting. This is not done anymore. On the other side, the choice of available colours allowed us to create, for the new extension, an interior design which perfectly reflects the corporate identity of Diako Mannheim. We managed to stick to the corporate design guidelines by combining several greys with a soft yellow (Pale Yellow K04.0.2) and a light blue (Powder Blue K22.2.4). From the point of view of brand recognition, this consistent colour scheme is essential”
As Dörte Krämer points out, the outstanding versatility of the Trespa® TopLab® allows for design concepts that minimise material disruptions. This results in elegant, harmonious interiors: “The situation was ideal: we were able to use the same TopLab® VERTICAL material for the wall panels, the sliding doors, the cabinet facings and the worktops. We were also able to pick up on this colour scheme for plinths and ceiling connections; in both cases, we used dark grey HPL. As for the deep anthracite of the panel core, which is left intentionally visible along the edges, it complements ideally the dark grey of the TopLab® worktops”.
HPL panels manufactured by Trespa are highly versatile: they are ideally suited for purposes that range from functional cabinetry and worktops to integrated wall and door solutions.” Dörte Krämer, project manager at Architekturbüro Roger Strauß
“A POTENTIAL UNLIKE ANY OTHER”: THE MANUFACTURER HAS HIS WORD
Back in 1985, GHK DOMO was created by a team of three as a conventional joiner’s workshop. In the meantime, the company belongs to the leading manufacturers of fully integrated interior solutions for cleanrooms and the healthcare sector. Jens Hoppmann, co-owner and Managing Director, puts it in a nutshell: “In the early Nineties, my father started to develop a system of modular wall panels that would remain removable at any point.
He was quick to recognise that the Trespa TopLab® VERTICAL collection had a potential unlike any other – for such an application in particular, but also for developing a whole range of complementary furniture. Initially, various technical hurdles had to be overcome – including the lack of suitable fittings and hardware. This did not prevent us from gaining expertise and expanding rapidly. To this day, know-how remains our main asset and our recipe for success”
Andreas Fladerer joined the company in 2007 as a Project Manager. He explains: “As far as operating theatres are concerned, we have succeeded in shaking up the German market rather thoroughly. In the meantime, 70% of our products are made from HPL manufactured by Trespa, and our focus on this material goes well beyond what a potential user will perceive at first sight – including on our website”. Jens Hoppmann describes the preliminary phase: “When we advise clients about the options at hand, we can point out that Trespa’s HPL products have a material profile that is uniquely well suited for functional environments in the healthcare sector. Andreas Fladerer adds: “No need to be shy here – for this type of application, TopLab® is unrivalled. Period.”
In operating theatres, reliable and enduring cleanability is crucial. Therefore, GHK DOMO values highly the availability of Trespa® panels in large formats and the resulting reduction in the number of joint gaps. “The closed surface of the TopLab® panels is another big advantage in that respect”, as Andreas Fladerer points out.
Jens Hoppmann goes into the details: “The EBC technology (Electron Beam Curing) sets Trespa apart, even in the specific field of High Pressure Laminates. Nobody can really compete with the smooth, closed finish this technology imparts to the material – Andreas Fladerer is right. This definitely makes the Trespa® TopLab® panels a superior alternative to standard HPL”. He mentions as well a fact that is often overlooked: wall panels made of stainless steel are not self-supporting, and need to be mounted on a carrier material. “More often than not, plasterboard is used for that purpose. But unlike HPL, plasterboard is sensitive to moisture. In the worst case, the plasterboard carrier will become moldy – something nobody wants to be confronted with in an operating theatre!”
The project is a prime example for the combination of visual appeal, practical advantages, technical excellence and outstanding cleanability that can be achieved by using HPL panels from the Trespa® TopLab® collection for our range of modular furnishing systems.” Jens Hoppmann, Managing Director at GHK Domo GmbH
AN IDEAL TECHNICAL PROFILE
Jens Hoppmann explains: “There can be no doubt for us: the TopLab® panels from Trespa are in a class of their own. This is true as well for their machinability. Therefore, it should come as no surprise that Trespa is GHK DOMO’s favourite partner”. He adds: “The Trespa panels are highly homogeneous – all the way to their core. In addition, they are manufactured to exacting tolerances. The panels can be cut and routed easily and precisely, resulting in utmost flexibility. For us, the versatility of TopLab® has several advantages. We can minimise the material mix by manufacturing very diverse components from just one material. In the operating theatres in Mannheim, for example, we used Trespa TopLab® VERTICAL not only on the walls, but also for the panels of the sliding doors, the exhaust enclosures and the frames used to install the monitors flush to wall. Reducing the material interfaces comes, by the way, with an added benefit: we need to worry much less about problems that can arise from differences in stretching behaviour.
He summarises: “The project is a prime example for the combination of visual appeal, practical advantages, technical excellence and outstanding cleanability that can be achieved by using HPL panels from the Trespa® TopLab® collection for our range of modular furnishing systems”.
Dörte Krämer expresses her own satisfaction: “The extension of the operating area at Diako Mannheim has been an allround success. Judging by the feedback we have received, we have met across the board the expectations of both management and users”. Hans-Jürgen Neugebauer is equally positive. He points out: “The coordination between the architectural firm, the users, the contractor and myself was smooth and efficient. All the specifications were duly met, we managed to stay on budget, and the project was completed within the predefined time frame – exactly as it should be
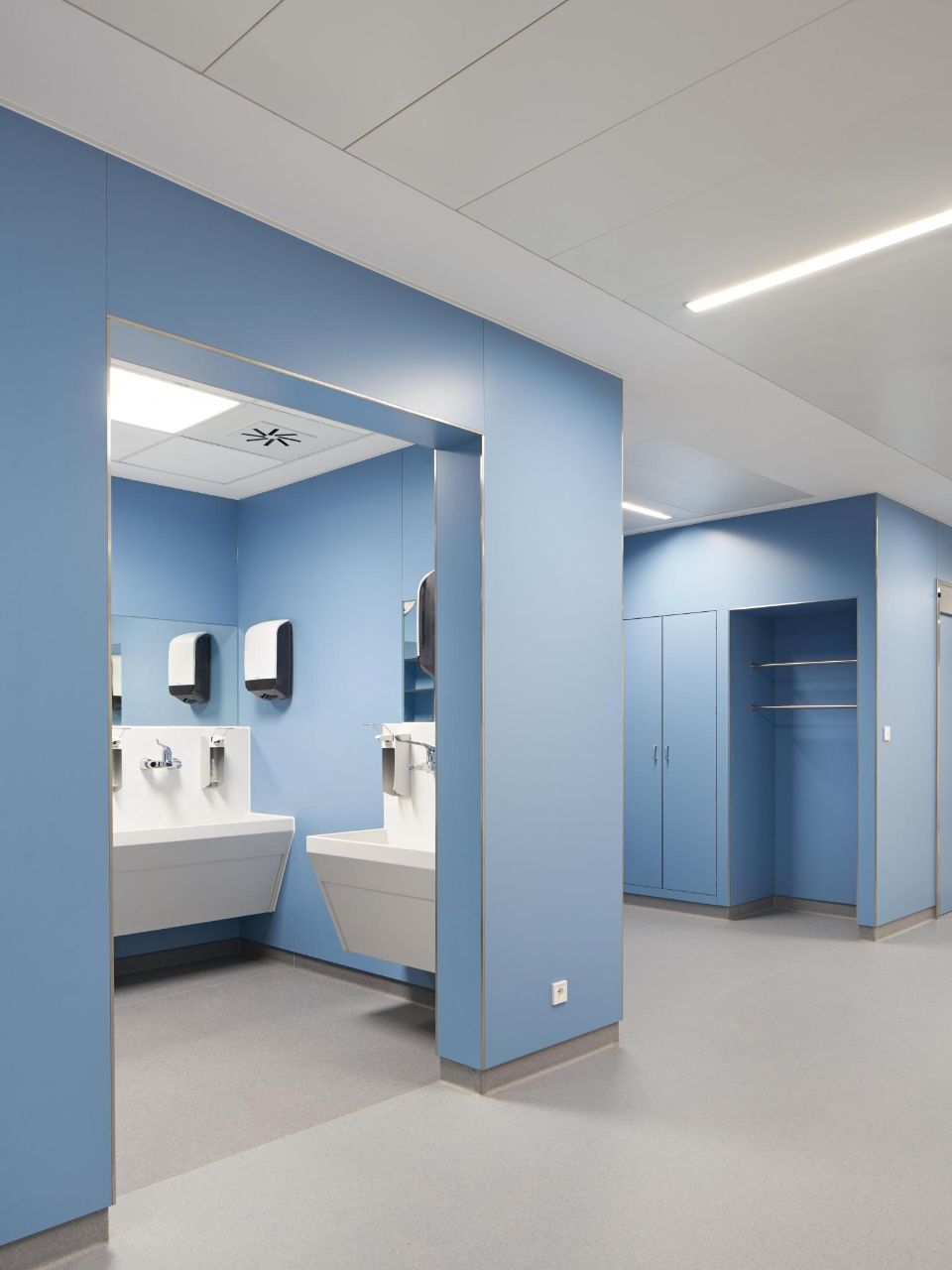
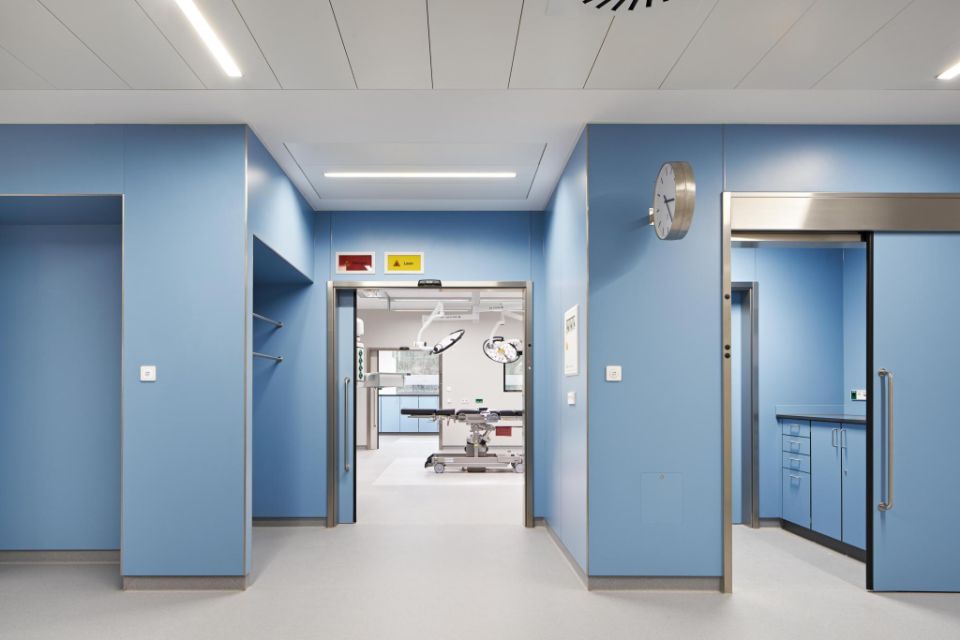
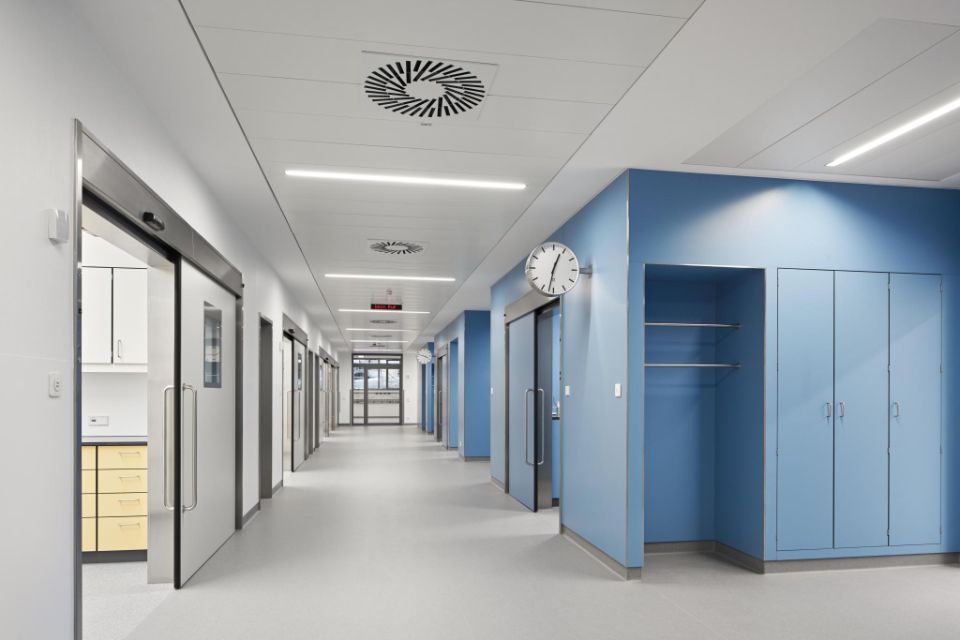