Health Center Hohenstein
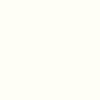
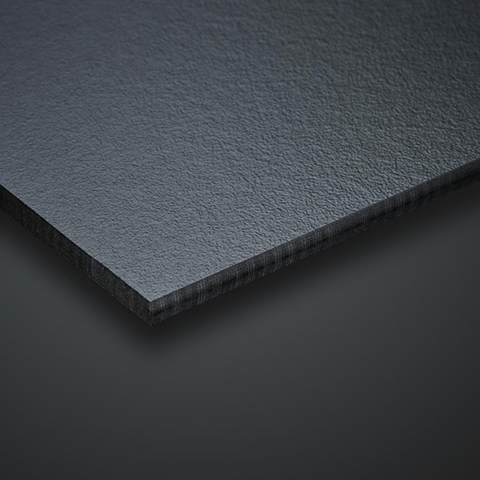
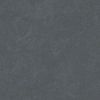.jpg)
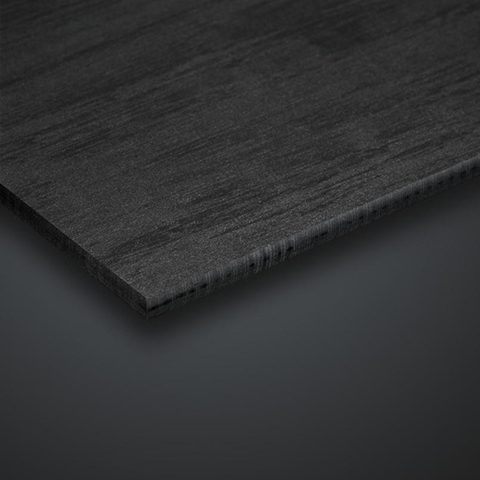
A promising venture : the community healthcare centre in Hohenstein
In the small city of Hohenstein, tucked away in the middle of the Swabian Jura, halfway between Tübingen and Ulm in Southern Germany, a recently built healthcare centre is breaking ground in more than one way. The innovative ‘PORT Gesundheitszentrum’, which has been endorsed and sponsored by the Robert Bosch Foundation, is using advanced technology – including an online eHealth platform – to provide the community with comprehensive medical services.
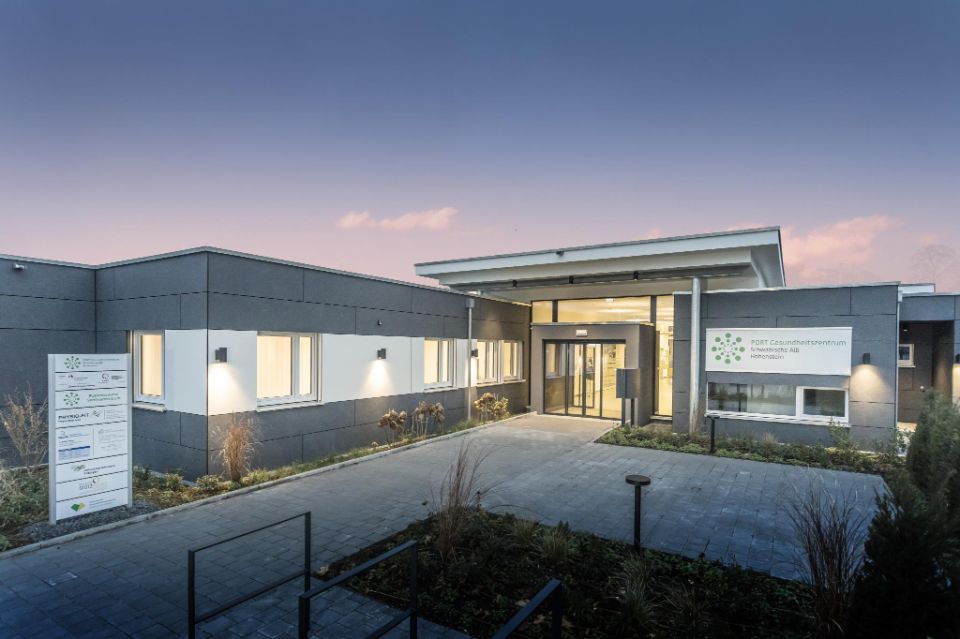
Everything has been done to firmly anchor the centre in its regional context as a crucial part of the local infrastructure. The project is pioneering not only an enhanced approach towards patient care, but a new spatial organisation and an unconventional overall concept as well. Last but not least, it offers an opportunity for young doctors to work in a rewarding, modern environment at a time when many among them are reluctant to practice in rural areas – a concerning development that has been affecting the German health system for a long time.
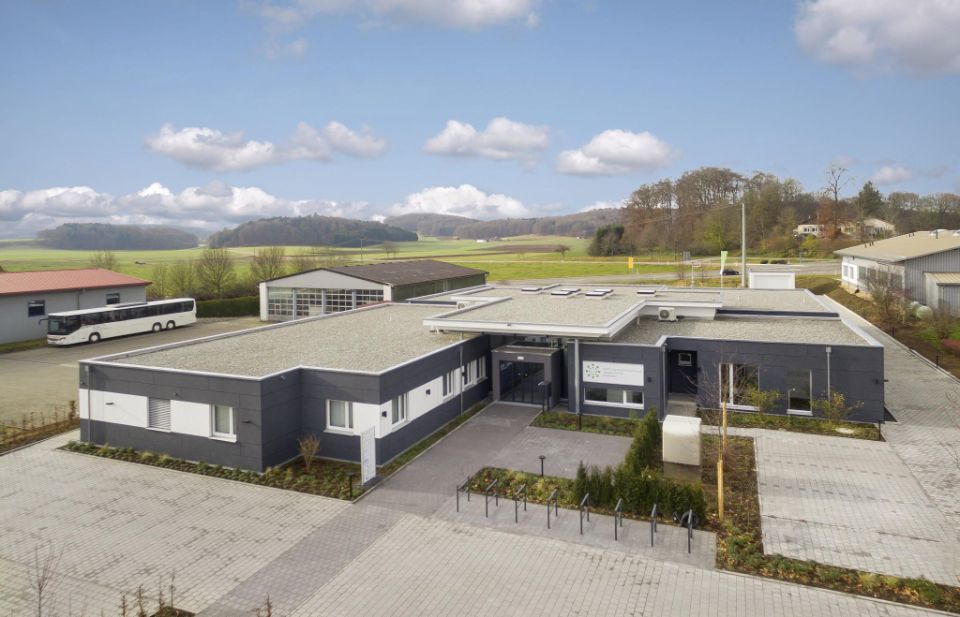
Sustainability meets social relevance
The healthcare centre was built and is being managed by SchwörerHaus, a well-known specialist for high-end manufactured and modular housing – a popular alternative to conventional ‘brick & mortar’ homes in Germany. Sustainability was, from the start, one of the main goals of the project: it combines modular wood frame construction with ventilated façades clad with Trespa® panels, which contain 70% natural fibres. In both cases, the project’s environmental profile benefits from renewable raw materials with grey energy requirements at the lower end of the spectrum.
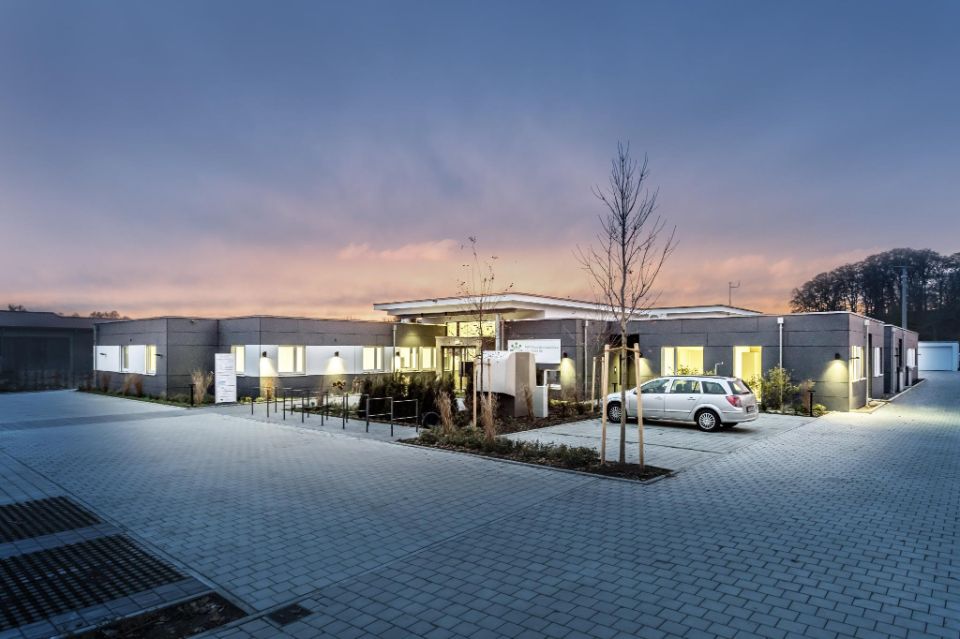
SchwörerHaus was founded in 1956, in the first phase of the German ‘Wirtschaftswunder’, the rapid post-war transformation of the country into Europe’s economic powerhouse. From the start, SchwörerHaus successfully pioneered the idea of upscale manufactured homes, and the family-owned company is a perfect example of the famed German ‘Mittelstand’ – medium-sized companies with a sharp focus on quality, innovation, client satisfaction and sustainable production processes.
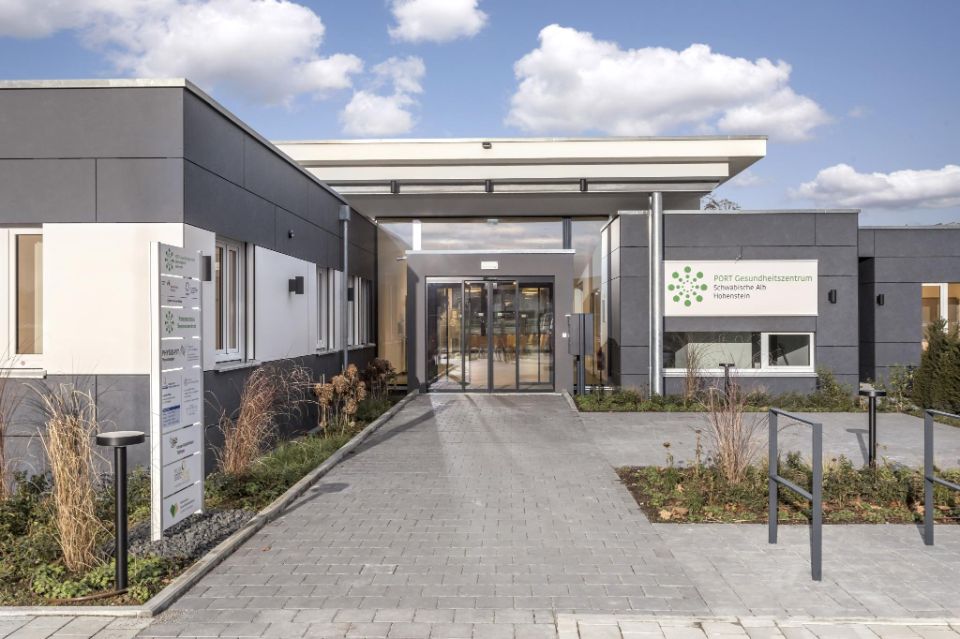
SchwörerHaus is headquartered in Hohenstein, making the PORT Gesundheitszentrum a perfect opportunity to showcase the company’s commitment to the community – and explore at the same time new market opportunities. Johannes Schwörer, the CEO of SchwörerHaus, was immediately receptive to the idea, according to Marketing Director Andreas Steiner. Since ‘Gesund Bauen’ (‘Healthy by design’) is one of the company’s central claims, getting involved with the healthcare centre and contributing to a much-needed upgrade of the social infrastructure in the region made immediate sense. As an added benefit, the company’s employees would gain access as well to first-rate medical services.
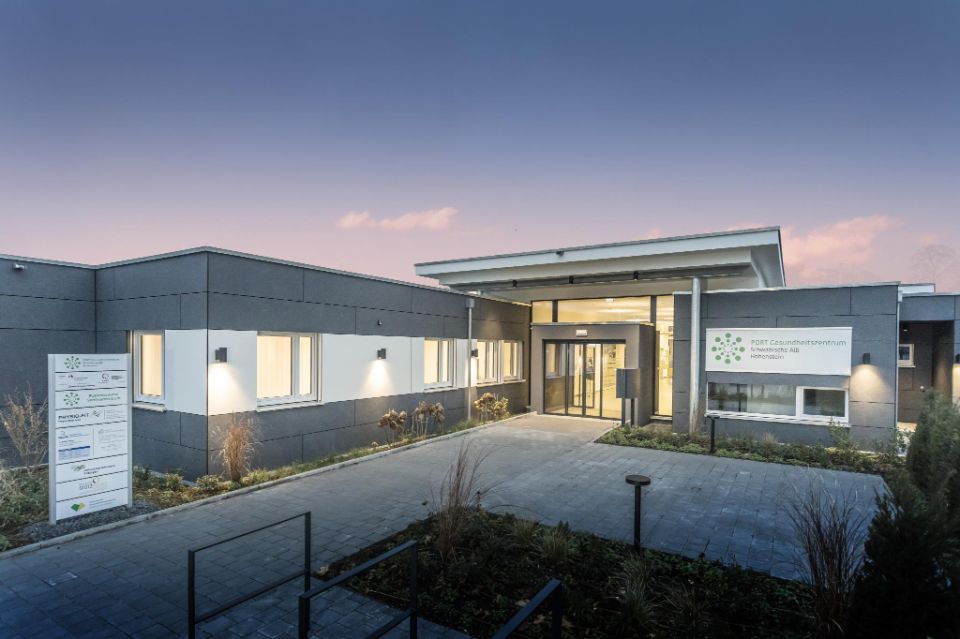
Prefab construction – a major building trend
Andreas Steiner points out: “We clearly wanted to test some innovative ideas. The building market for private houses is certainly large, but it is neither boundless nor expandable. At the same time, we anticipate a sharp increase of the demand for fully prefabricated building modules in the near future”.
He explains: “One of the triggers for this fairly recent trend has been the growing popularity of the ‘tiny house’ concept. This is a global phenomenon, and Germany is certainly no exception. The idea is to supplement – or even replace – conventional housing with very compact, but well-equipped units, and it is gaining traction surprisingly fast. As an answer, we have developed our highly versatile ‘FlyingSpaces’. They can be used to enlarge or complement an existing house – for example to accommodate a caregiver or a nurse in the case of elderly people. They will work just as well as an easily set up, small yet luxurious and cost-effective holiday house – or even as a permanent home”. In the latter case, the tiny house concept holds considerable appeal for those among us who favour a ‘less is more‘ approach and want to go back to a radically decluttered lifestyle. For many of them, dispensing with a mortgage and similar, long-term obligations usually associated with conventional home ownership comes as a bonus.
In such cases, the principles of modular construction combine several decisive advantages. According to a study that consulting company McKinsey published in 2019, modular buildings can be completed in up to 50% less time than conventional ones; depending on the project, modularity can also lower the building costs per m². For the FlyingSpaces, SchwörerHaus has been able to tap into the company’s know-how to offer sophisticated solutions: the completely prefabricated wood-frame modules can be extensively tailored to each client’s preferences. They are supplied as self-contained, fully equipped and move-in ready units. Andreas Steiner underscores: “The modules are also very energy-efficient, thanks to high-end thermal insulation that is on par with our regular SchwörerHaus homes: both our FlyingSpaces and our modular houses comply with the German energy efficiency standard ‘KfW Effizienzhaus 55’. This means that, when compared with the benchmark value, they need only 55% of the primary energy. Similarly, the heat transfer coefficient is only 0.7, versus 1 as defined by the standard”.
Thoroughly modular: the healthcare centre paves the way
Franca Wacker, the company’s in-house architect, was in charge of the PORT Gesundheitszentrum project. She comments: “The modularity of our FlyingSpaces is ideal when it comes to this kind of non-residential building. Essentially, this is a new market segment where our expertise in modular construction is immediately applicable. Accordingly, the potential synergies are highly attractive”.
Modular construction is at the core of the architectural concept: the healthcare centre is entirely based on the FlyingSpace design, even if, at the time, some of the modules could not be prefabricated, as the dedicated production hall at SchwörerHaus was still in the final stages of construction. A centrally located atrium acting as a ‘plaza’ connects the various modules.
Franca Wacker points out: “Each medical office has its own module. Since the centre is designed to be flexible and readily expandable, the modular principle is indeed very practical. We can add office space fast and easily – and the process is remarkably cost-efficient’. Andreas Steiner adds: “As the prefab modules have been designed to be stackable, we can also expand vertically. Three-storey buildings made of FlyingSpaces are technically feasible, and from the start, the healthcare centre was planned as a two-storey structure. The space for the elevator and the staircase is already part of the floor plan.
Trespa® cladding panels – a natural choice
“I have been familiar with the Trespa® product range for some time already, as I used Trespa® panels at an earlier point of my career”, explains Franca Wacker. “Back then, the product had been very convincing – and it still is. The panels are enduring, high-quality and they have been around for quite a while: this is truly a tried-and-tested product. At SchwörerHaus, we use Trespa® Meteon® panels regularly on our modular houses, mainly to create colour or material contrasts. When compared with more conventional façade materials, the HPL panels manufactured by Trespa come with several significant advantages – especially in terms of durability, high weather resistance and outstanding colour stability. Easy maintenance is an additional benefit for house owners: hosing down the façade from time to time is all it takes”.
Regarding the PORT Gesundheitszentrum, she explains: “Here, the situation was obviously different. Fibre cement panels could have been an alternative, but the material can be less than easy to deal with on site, and with fully prefabricated modules that include factory-installed cladding, some damage could have occurred on the modules’ way to their final destination. Admittedly, this could not have happened this time, as the cladding was put in place on location due to temporary constraints”. Andreas Steiner comments: “Since our dedicated production hall was still under construction, the Trespa® panels had to be installed on the building site. But this will soon be a thing of the past, as we are aiming at fully integrated prefabrication”.
“For the sub-frame of the façade, we used wood”, adds Franca Wacker. “A local company, Holzbau Moser in Hirschfeld, was put in charge of the façades. They cut the Trespa® Meteon® panels to size and installed them directly on location. Wood for the sub-frame was indeed the way to go, and everything went smoothly. Therefore, we intend to stick to a wood sub-frame when cladding becomes part of the prefab process”.
Franca Wacker goes into the details of the material selection: “We started with a variety of samples which we had ordered from Trespa. At the same time, we submitted a panel to a ‘destruction test’ that failed convincingly – which was exactly what we had hoped for! In addition, I knew from my previous experience that cutting, drilling and, if needed, sanding the edges of Trespa® Meteon® panels will yield clean and accurate results. This allows for a precise fit and for even gaps between the panels, something I highly value. All these factors made it easy to bring on board our CEO, Johannes Schwörer. He readily approved our material choice and involved himself in the selection of the two panel colours we wanted to combine. Together, we opted for NA16 Belgian Bluestone – a panel with a finish reminiscent of natural slate – as the main colour. We complemented it with contrasting white panels (A05.0.0 Pure White) as a lateral extension on some of the windows”.
Trespa and SchwörerHaus: a collaboration with a bright future
Following the completion of the healthcare centre, the feedback so far has been very positive. As Franca Wacker points out, the company has even received several enquiries from potential new clients. She explains that in general, the concept of the fully modular tiny house has been a recurring topic in the media over the last 2-3 years, thus generating additional, positive exposure for the principle of prefab modules. “Our CEO is keen to further increase our presence in the new market segment to which the PORT Gesundheitszentrum belongs”, she comments.
“In the future, I can see us offering the full range of Trespa® Meteon® colours and decors for our FlyingSpaces. Since – as I already pointed out – we currently offer Trespa® panels as an option for our modular private houses, multifamily homes and non-residential buildings, this would be logical”.
“For the Flyingspaces in all their variants, which will shortly leave the production hall at SchwörerHaus fully prefabricated and equipped for move-in ready delivery, Trespa® Meteon® panels are an ideal cladding solution”. Franca Wacker adds: “We offer a wide range of finish options for the façades. As a standard, the modules come in a render finish, but the optional possibilities are manifold. Basically, the FlyingSpaces share the same options that are available for our modular houses – including wood sidings in several variations, ceramic tiles and even BIPV (Building Integrated Photovoltaics)”.
She summarises: “Trespa is well-positioned among these material options. The diversity of the available colours, decors and finishes is fully in line with our own emphasis on offering bespoke solutions for every taste. In addition, the durability and resistance of the Trespa® panels contribute to the overall enduring quality of the FlyingSpaces – a key aspect of the SchwörerHaus company philosophy. Therefore, the potential for further expanding our cooperation with Trespa is definitely strong”.